Little Leaf Farms maximizes space and efficiency with semi-automated storage and retrievel system
Quadrupling in size since 2015, Little Leaf Farms built a sophisticated, sustainable indoor growing facility on a 10-acre development that has changed the local lettuce landscape. Hydroponically grown greens without pesticides, harmful chemicals, or GMOs, is planted, nourished, harvested, packed in containers, and labeled- completely hands free. It’s delivered to local grocery stores within 24 hours of harvest, producing high-quality, ultra-fresh lettuce for New England year-round.
Challenge
Once the containers are filled with freshly cut lettuce, workers in the manufacturing area immediately pack them into cases. The cases get stacked into pallets, shrink wrapped and moved into a height-restricted 4,300 sq/ft cooler. Little Leaf Farms needed an efficient and accessible way to store and move the two million plus packages of lettuce the facility produces each month and deliver to a growing number of local retailers daily. Installing pallet flow racking was an obvious choice to use for the expanded new cooler that supports their one million square foot greenhouse. So, they sought quotes for racking from several vendors. Our partner and dealer, Abel Womack, however, proposed a different solution.
We knew that Little Leaf Farms were serious about sustainable practices. So, rather than quote pallet flow racking, we presented a more unique solution that concentrates the storage footprint of their climate-controlled space and reduces energy costs.
Carl Rezendes, Account Manager at Abel Womack
“We understood Little Leaf Farms’ process and knew they were serious about sustainable practices. So, rather than quote pallet flow racking, we presented a more unique solution that concentrates the storage footprint of their climate-controlled space and reduces energy costs. We demonstrated how Radioshuttle®, a semi-automated pallet shuttle system, increases operational efficiency by utilizing the full height of the building and deep lane racking maintains selectivity between all levels. The lanes are fed shrink-wrapped pallets by lift trucks. Easily operated via a hand-held remote control, pallets are loaded/unloaded into lanes, moving with more than twice the speed of conventional rack. It not only increases productivity, but it minimizes product damage by reducing product touches, and decreases labor costs”, says Carl Rezendes, Account Manager at Abel Womack.
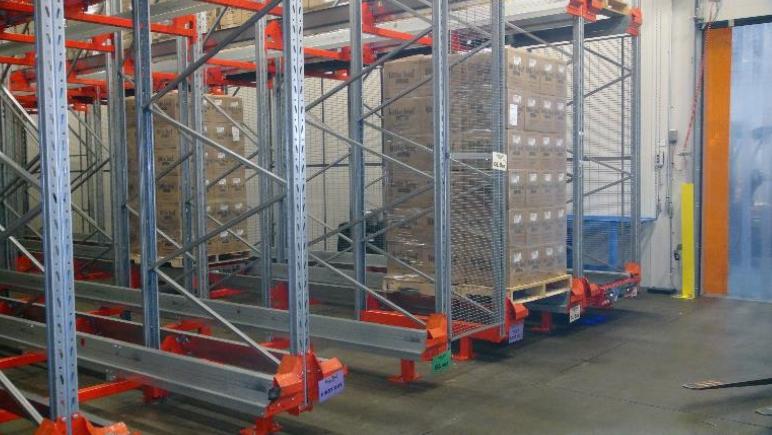
Solution
Little Leaf Farms implemented Radioshuttle® in their cooler consisting of eight lanes, two levels high, and 17 pallets deep. This provided a total of 238 pallet positions on the rails. Since they’re dealing with perishable products, the workflow configuration used was first in-first out (FIFO). Radioshuttle comes with a work platform, battery charging station and an extra set of lithium-ion batteries to power the system for a minimum of 14-hour shifts. There is a learning curve, but the system is easy to operate. Plus, Radioshuttle® works in all temperature zones, like a 34-degree ͦF cooler.
When initially comparing Radioshuttle to traditional pallet flow racking, one of the key differences Abel Womack pointed out is maintenance. Pallet flow racking rollers require service, which in turn, affects productivity. With Radioshuttle’s reliable and durable structure, there is virtually zero maintenance.
“The storage efficiency we gained from Radioshuttle® has increased our pallet capacity six-fold.”
Mike Yagodzinski, Corporate Materials Manager, Little Leaf Farms
Result
Providing engineering services, project management, and installation, Abel Womack worked with this thriving indoor growers to streamline their shipping and receiving operations as efficiently and cost effectively as possible. Little Leaf Farms initially had seven SKUs and two carts, but soon after added a third cart with no disruptions. If they add additional greens to their mix of offerings in the future, Radioshuttle® provides the flexibility to easily accommodate more SKUs.
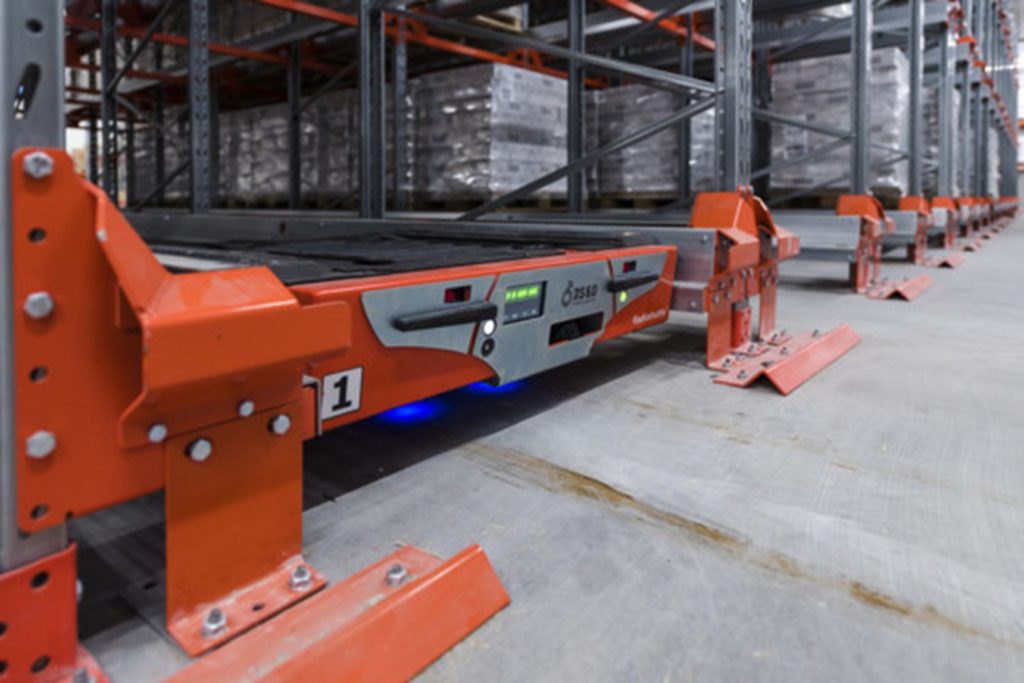
Mike Yagodzinski, Corporate Materials Manager at Little Leaf Farms said, “The storage efficiency we gained from the Radioshuttle® System has increased our pallet capacity six-fold. It also enables us to load trucks faster and we don’t have to worry about downtime.”
He also mentioned as Little Leaf Farms expand operations along the east coast the new facilities will all be equipped with Radioshuttle®.
Listen to Little Leaf Farms here, explaining what Radioshuttle® has done for them.
Text, image and film: Abel Womack